Mixers and mixing systems for powders or grains
In mixing facilities, we start with dry powdered (flour) or granulated products, and we mix them homogeneously for later use or directly for bagging. It is also possible to add liquids such as water, fragrances, oils, fats, etc.
We have versions of mixers adapted for each type of product and industry.
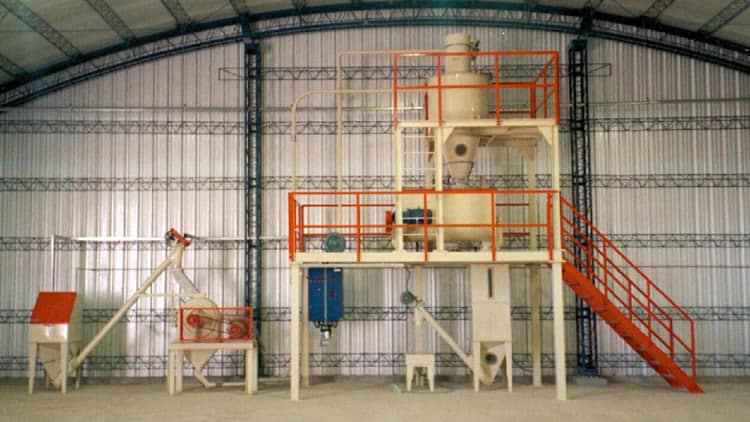
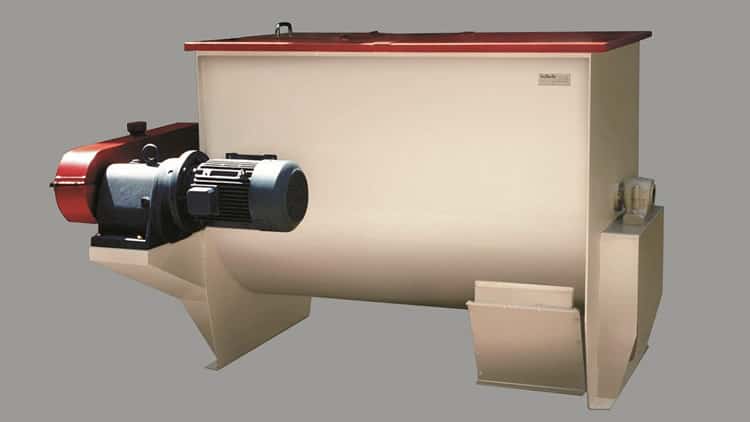
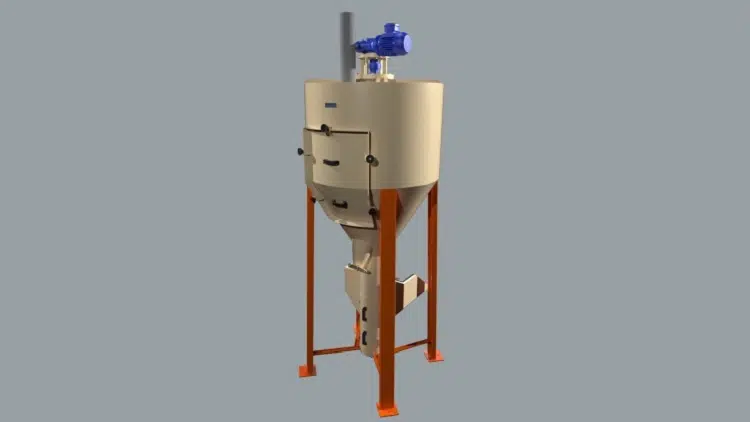
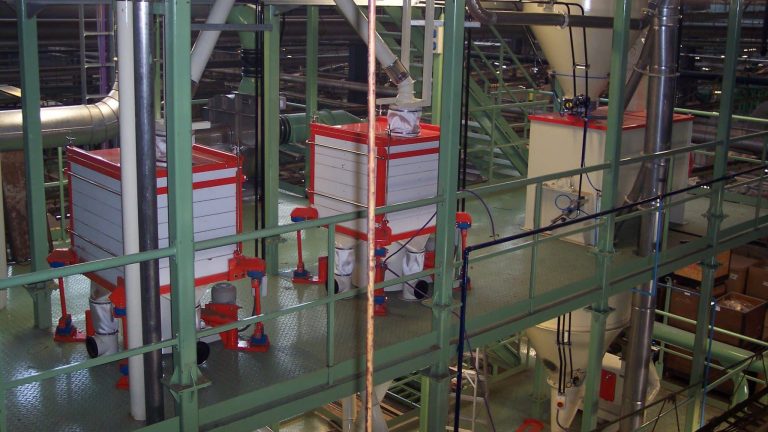
According to the needs, the facilities can range from just the mixer to turnkey high-capacity, automated mixing plants. We use them for food, chemicals, cement, minerals, etc.
Types of mixers
Fundamentally, mixers can be classified as either “batch” type or “continuous” type.
- Batch mixers: In this type of mixer, products are added, mixed for a certain time, and then discharged.
- Continuous mixers: These mixers must be continuously fed with each component proportionally to its required percentage in the mixture. The components enter from one end of the mixer and exit perfectly mixed from the other.
Prillwitz mixers
In mixing systems, speed is very important, which is why all our mixers are high-speed. Among them, we primarily offer the following:
- HIT helical auger mixer: A horizontal batch mixer with a rotor with opposite-pitch helical screws. Very fast. Achieves high-quality mixing in a few seconds
- MVA vertical mixer: A batch mixer with a vertical overflow screw. Intermediate mixing qualities are achieved. Its main advantage is that it does not require peripheral installations
- MIT high-speed paddle mixer: A horizontal continuous mixer with paddles. It requires a high level of automation but achieves high-quality mixing in a small space.
Ensayo: ¿Cómo se evalúa la calidad de una mezcla?
A mix consists of at least two components, which are typically completely separate at the beginning of the mixing process. The goal is a homogeneous distribution of the components. Even the smallest portions of the mix should, as much as possible, have a composition corresponding to the entire mix.
To evaluate the quality, samples should be taken from different areas of the mixed mass and analyzed. The appropriate sample size depends primarily on the intended use of the mixture. For example, sample sizes are smaller if the mixture is intended for small tablets in pharmaceutical production compared to animal feed.
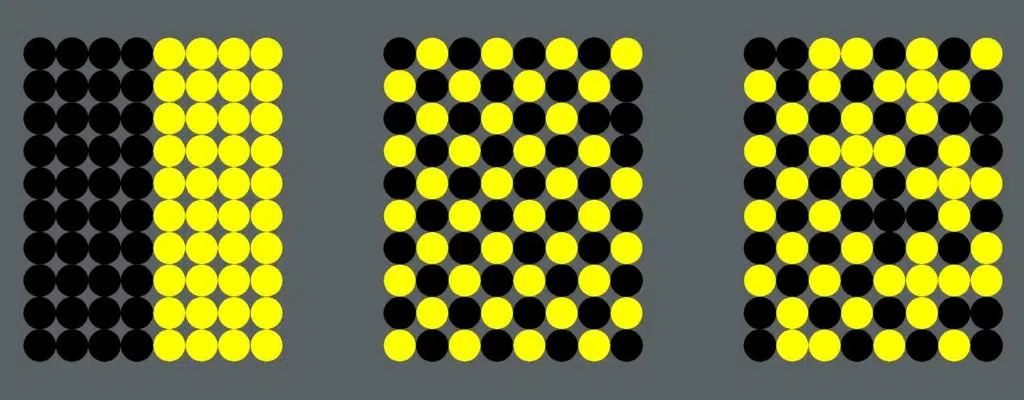
Ideal mixing homogeneity would be achieved when the concentration X of a component is the same in all individual samples that we could take. Ideal homogeneity does not occur in real mixing systems, and depending on the physical characteristics of the products to be mixed and the type of mixer chosen, we can more or less approach the ideal.
The standard deviation of concentrations in individual samples relative to the target concentration is a measure of the quality of a mixture.
For the mathematical model of the mixture, it is irrelevant whether the concentration of each individual sample varies up or down. Therefore, as a measure of the quality of the mixture, the squared standard deviation is used. In summary, the value that will give us the accuracy of a mixture of certain components with certain physical properties, with a certain sample size, and with a certain mixer running for a certain time, will be the variance of the sample concentrations:
Where:
σ²(t) = Variance after a certain time
t n = Number of samples
Xi = Ideal concentration
Xs = Measured concentration
Main mixer models we can supply
1- HIT helical auger mixer
The Hit rapid mixer has been specially designed for mixing large volumes of product in 3 to 5 minutes.
This mixing machine has a horizontal rotor with two double-helix screws or ribbons that rotate, transporting the product in opposite directions, thus mixing the different components. Our mixing equipment also stands out for its speed during emptying: with the standard discharge version at one end, the hopper is completely emptied in 20 seconds. With the quick-discharge version along its entire length, emptying is completed in 6 seconds
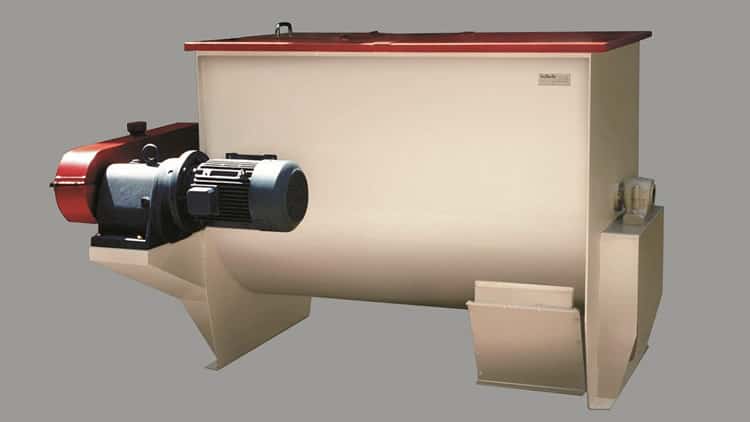
Prillwitz has perfected its high-speed mixers by incorporating a precise double helical screw system that ensures perfect homogeneity in the mixture.
Its robust construction makes our mixers an essential item when mixing all kinds of products and ingredients, from the most abrasive like minerals to those with difficult flow properties like flours.
For those who need precise weight control, Prillwitz provides mixers with scales and weighing systems, to which an optional recipe and production control system can be added.
Commonly used for mixing ground cereals in the production of balanced feed for cattle, sheep, pigs, and other animals.
Once the mixture is produced, we also provide silos, bagging machines, and big-bag fillers to complete the process.
2- Vertical mixer MVA
Mixer with vertical screw, integrated into a feeding and discharging system, allowing it to be operated without additional installations. Widely used in the plastic industry for the preparation of Masterbatch additives.
The MVA mixer is specially designed to mix products with similar specific weights with the possibility of also adding liquids.
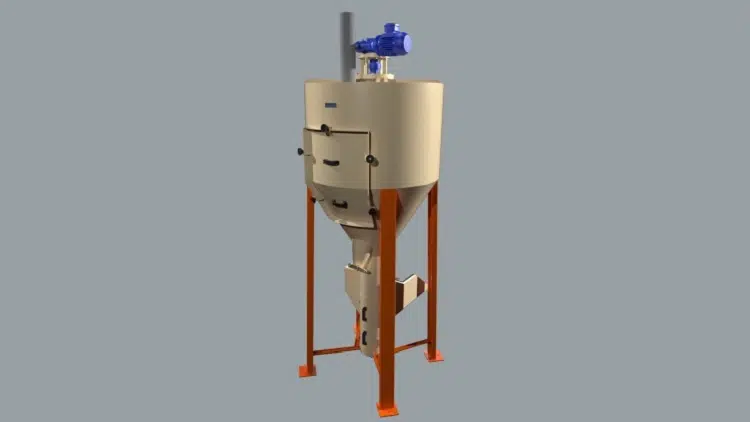
Due to the way the mixer is fed and discharged, it is generally used autonomously without additional installations.
Feeding the mixer: The most common way to feed it is through a lower inlet hopper, usually adapted to receive the contents of bags. It has a grid that prevents the entry of foreign materials.
Discharge of the mixer: Discharge occurs through a hopper located on the opposite side of the feeding. It has a valve, which is usually manual but can also be electropneumatic as an option. Mixing times: They depend on the product and the % of liquid added but are generally always less than 10 minutes.
3- Continuous high-speed paddle mixer
MIT Our new MIT paddle turbo-mixer is designed for the continuous mixing of powder or granular products with or without the addition of liquids.
Due to the high speed of its horizontal paddle rotor, a high mixing quality is guaranteed, even when the products to be mixed have very different characteristics.
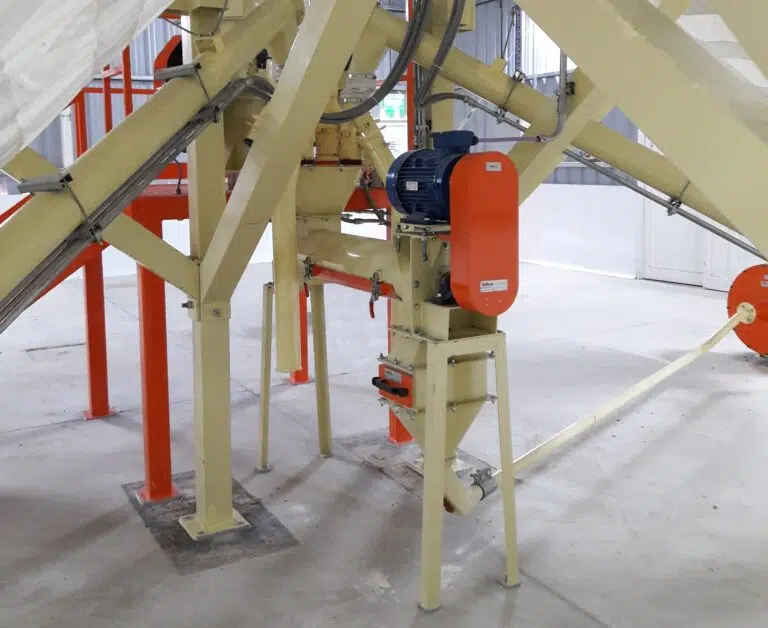
Mixing paddles: The mixer rotor has fixed-angle paddles. They can be comfortably replaced in case of wear. In smaller mixers, the replacement of mixing paddles is done from one end. In larger ones, there is a door around the circumference and the entire length of the machine, allowing replacement through it.
Examples of possible mixing installations of different complexity and application
The following batch mixing installation is a simple setup commonly used for intermediate capacities. For this type of installation, the HIT double screw horizontal mixer is very useful.
To simplify further, it is possible to feed the mixer directly through its hinged safety-grill cover, thus avoiding
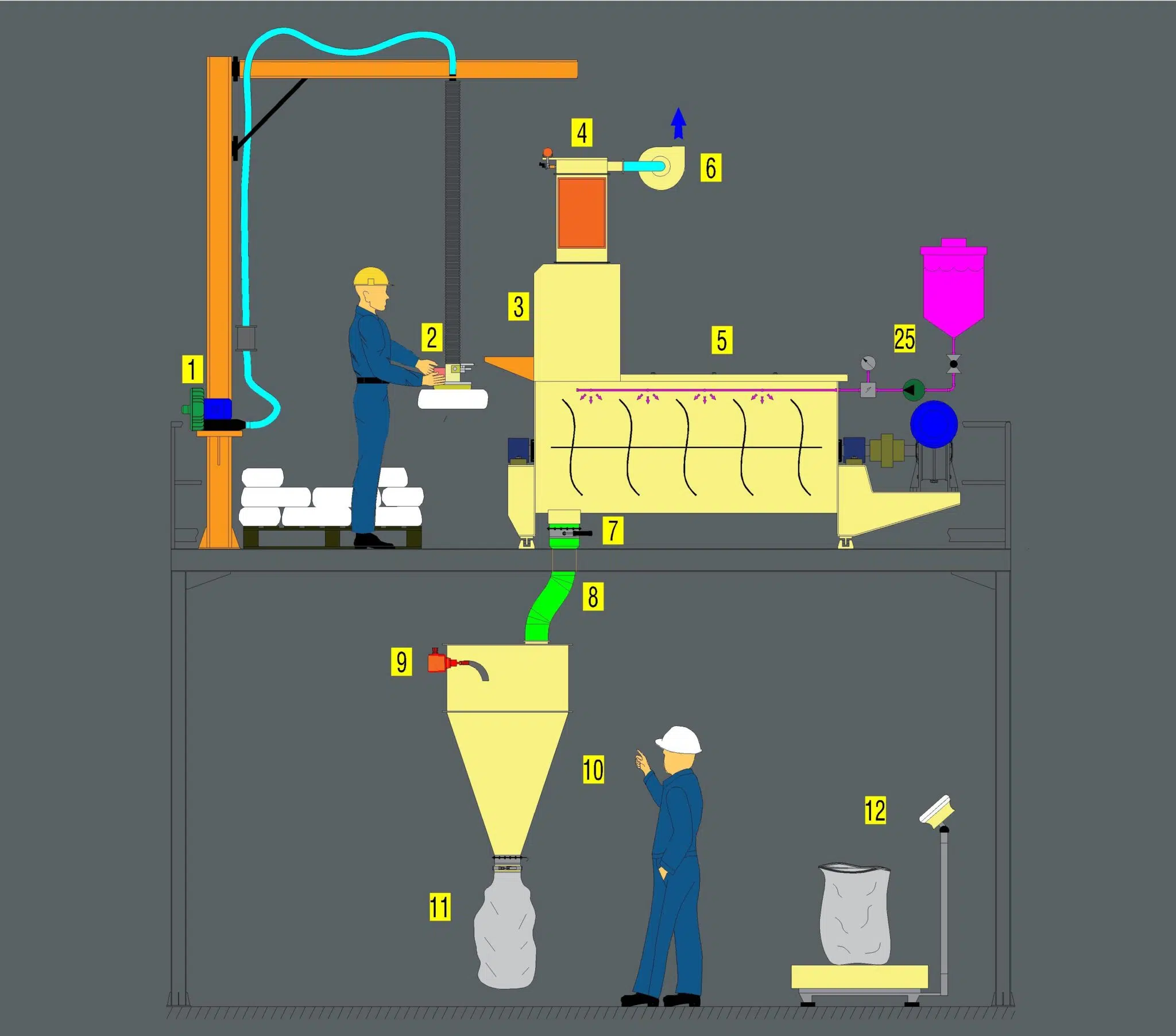
The following batch mixing installation is a high-capacity setup, where the dosing of each raw material is automated in the proportion required for the mixture. Note that a scale is placed on the HIT horizontal mixer to weigh each component automatically.

The following mixing installation is continuous. This means that each component is added in the proportion by weight per unit of time required for the final product. For mixing, we use the continuous paddle mixer MIT. Another commonly used component in this type of installation is the gravimetric doser DMCAg, which feeds a precise amount of kg/h to the mixer.
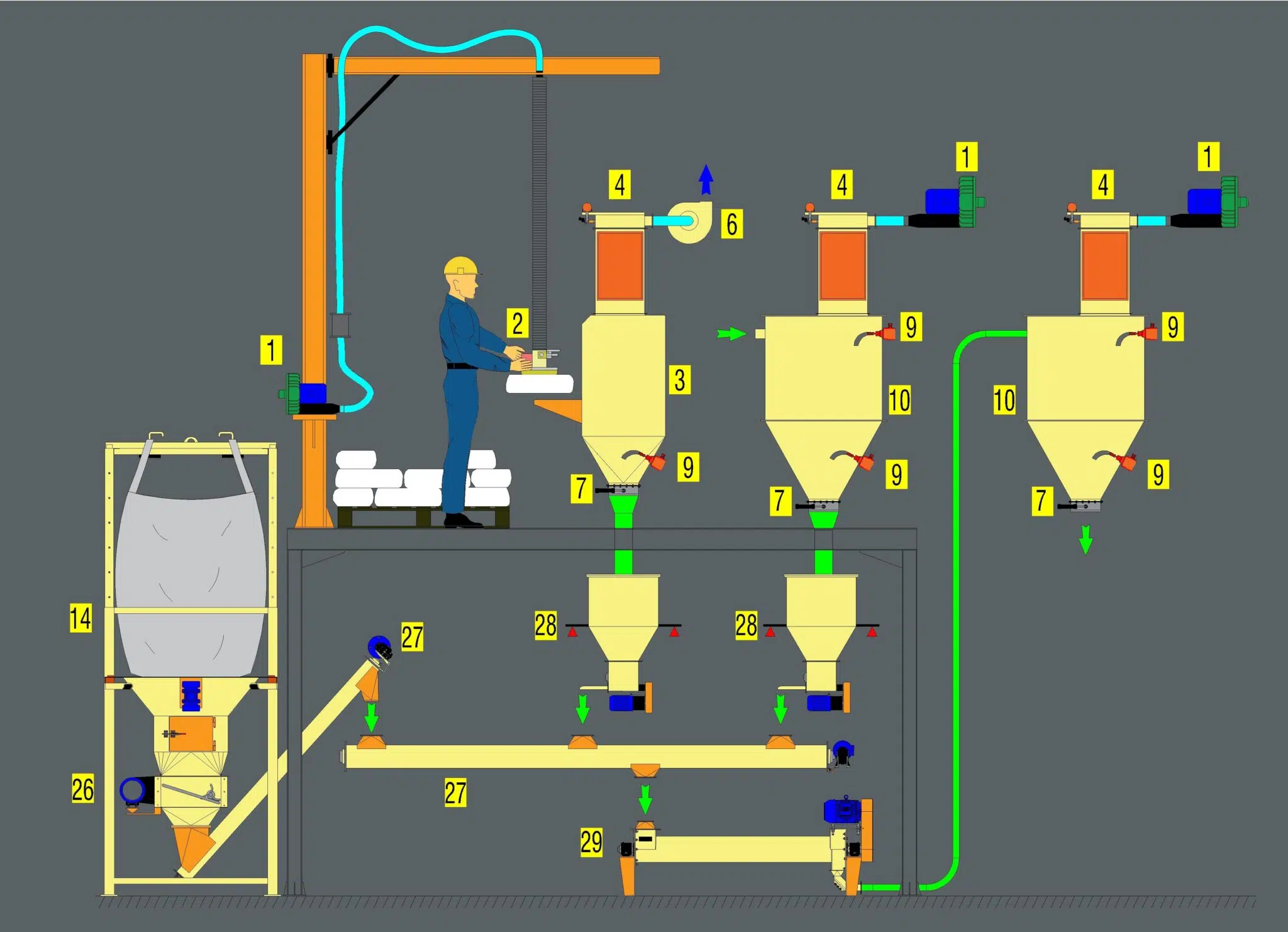
03- Bag cutting hopper
04- HDFA filter
05- HIT mixer
06- HT fan
07- Butterfly valve
08- Downpipe
09- Level sensor
10- Buffer tank
11- Strap for bag placement
12- Floor scale
13- ASR compressor
15- Rotary valve
16- Weighing hopper
17- Fluidizer
18- Manual valve
19- Silos
20- HAM extractor
03- Bag cutting hopper
04- HDFA filter
05- HIT mixer
06- HT fan
07- Butterfly valve
08- Downpipe
09- Level sensor
10- Buffer tank
11- Strap for bag placement
12- Floor scale
13- ASR compressor
15- Rotary valve
16- Weighing hopper
17- Fluidizer
18- Manual valve
19- Silos
20- HAM extractor
21- Storage/visor
23- Visor
24- Conveyor belt
25- Liquid dosing
26- DSE delumper
29- MIT mixer
What should we know to choose the most appropriate mixer?
To design a mixing installation, we need to know at least the following:
- Granulometry (Microns) and apparent specific weight (kg/dm3) of each dry component.
- Data on each liquid component: Corrosiveness, viscosity, etc.
- % of each component in the mixture.
- Packaging from which each component will be introduced into the system: Bag (kg), big bag, silo, etc.
- Required mixing capacity (Kg/h).
- Destination of the mixture: Bag (Weight and type), silo, production tank, etc.